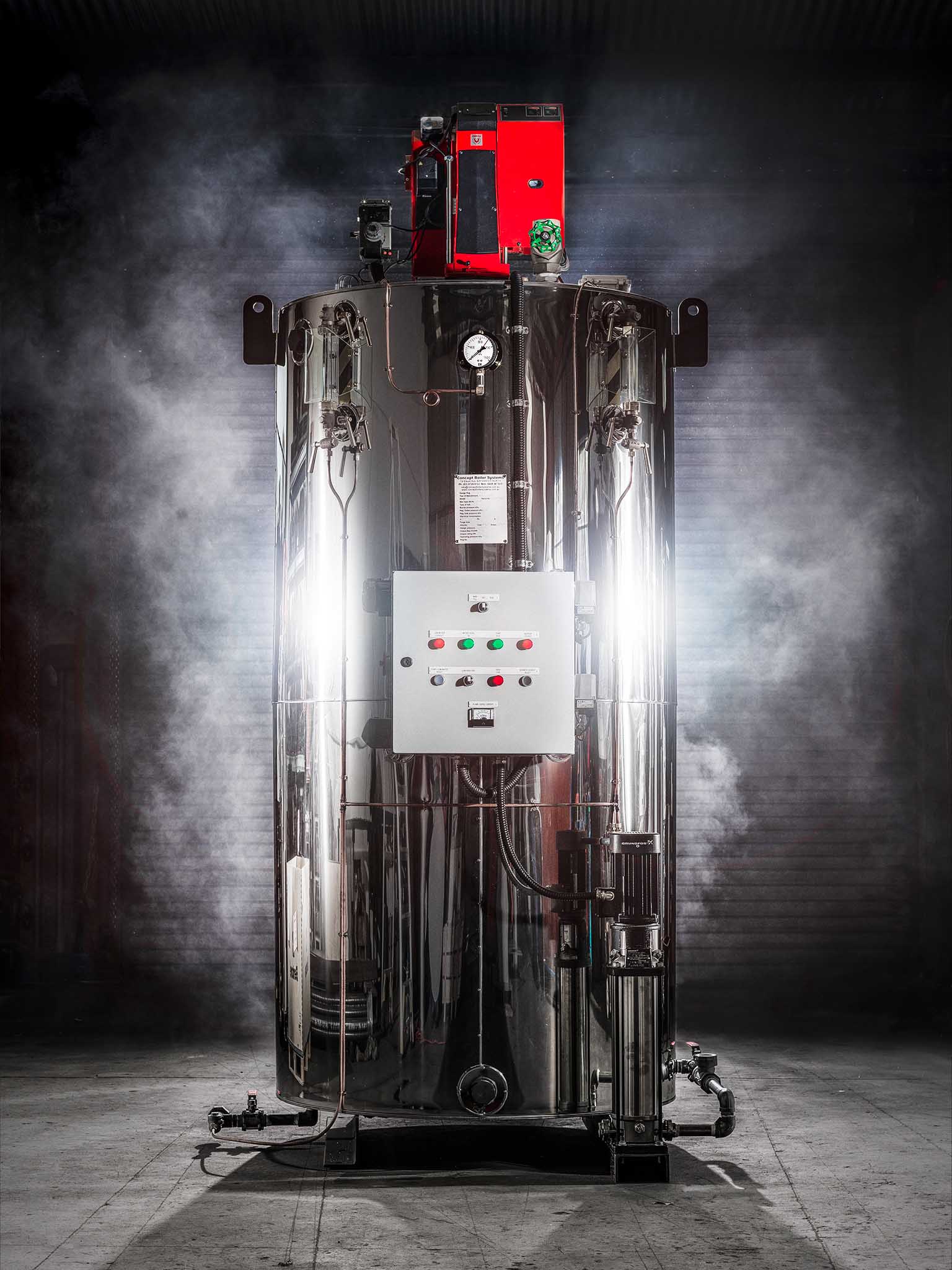
Table of Contents
- How Boilers Work
- Types of Boilers: Firetube vs. Watertube
- Components of a Boiler System
- Common Boiler Applications
- Watertube Boilers: The Safest Design?
- Boiler Maintenance & Monitoring
How Do Boilers Work?
Steam boilers are essential devices that generate steam by heating water to its boiling point under pressure. This process involves the use of a combustible fuel source, such as natural gas, LPG or electricity, depending on the boiler setup.
Types of Boilers: Firetube vs. Watertube
The operation of a steam boiler depends significantly on its design, which can be classified mainly into firetube and watertube boilers. Generally, Watertube steam boilers are a superior choice for most facilities, offering improved safety, efficiency and flexibility.
Each type has distinctive characteristics and uses, making them suitable for different applications.
- Firetube Boilers: Firetube boilers are named for their design feature where the combustion gases flow through tubes that are surrounded by water. These tubes are housed within a sealed container or shell. As the fuel burns inside the tubes, the heat is transferred through the tube walls to the surrounding water. This heat exchange process gradually increases the water temperature until it turns to steam. The steam generated in firetube boilers is often used in operations where pressure fluctuations are minimal.
- Watertube Boilers: In contrast, watertube boilers contain water within the tubes and heat the water externally. The tubes run through a furnace where the combustion process occurs, and the heat generated surrounds these water-filled tubes. The external heating of the water in the tubes allows watertube boilers to generate steam at much higher pressures. This makes watertube boilers ideal for industrial applications requiring high-pressure steam, such as power generation plants and large manufacturing facilities.
Both types of boilers have their advantages and are chosen based on the specific requirements of the application, such as steam capacity, pressure demands, and available space. Firetube boilers tend to be more compact and easier to install, making them popular in small to medium-sized facilities, while watertube boilers are favored in applications where high-pressure steam is crucial and space considerations are less restrictive.
By understanding the fundamental differences and operational mechanics of these boilers, facilities can better decide which boiler type will most efficiently meet their steam production needs.
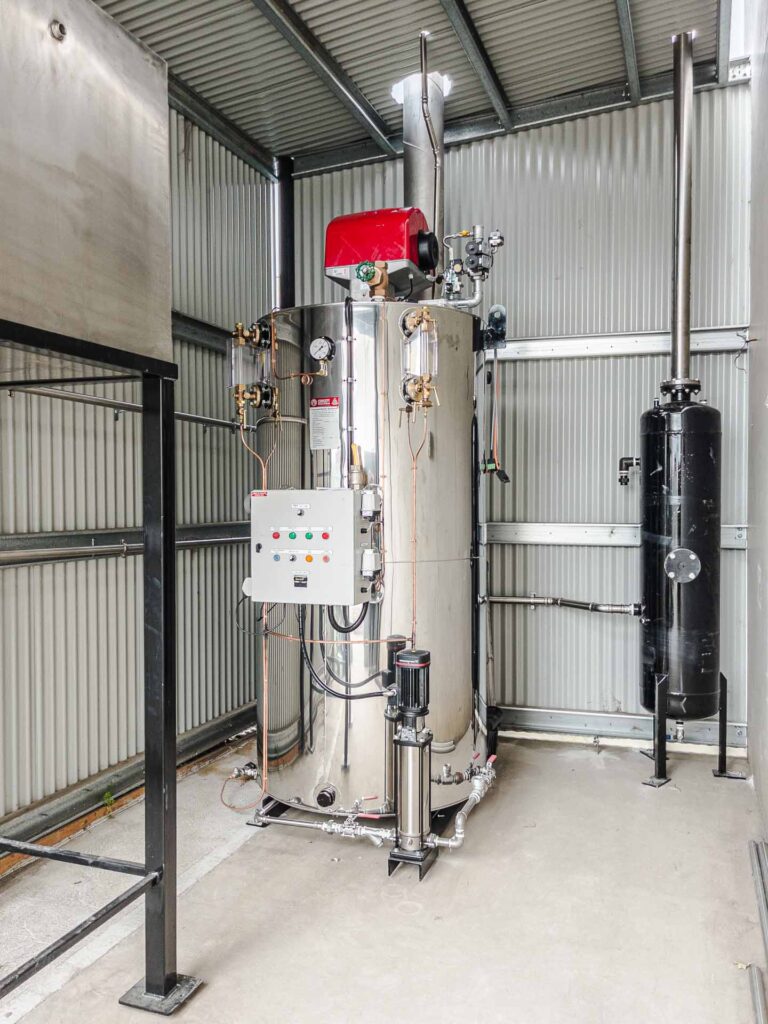
Components of a Boiler System
A boiler system comprises several critical components that work together to produce steam efficiently and safely. Here’s an in-depth look at each component’s role within the system:
- Pressure Vessel: The core of a boiler, the pressure vessel, is robustly constructed using high-strength materials such as steel to withstand high temperatures and pressures. This vessel contains the water that turns into steam as the boiler operates.
- Burner (Combustion System): The burner is where fuel (such as natural gas, propane, oil, or coal) is mixed with air and ignited to generate heat. This heat is then transferred to the water through the walls of the pressure vessel or tubes depending on the type of boiler.
- Tubes: In watertube boilers, water flows inside the tubes which are heated externally. In contrast, firetube boilers have hot gases flowing through the tubes, surrounded by water. These tubes are critical for the efficient transfer of heat to the water.
- Control Panel: This component allows operators to adjust boiler settings like temperature and pressure, critical for maintaining optimal performance. Advanced control panels provide detailed analytics that help in monitoring the boiler’s operation.
- Feedwater Tank: Here, the make-up water for the boiler is stored and pre-treated. The water is often pre-heated in this tank, and chemicals are added to remove oxygen and other impurities, which helps protect the boiler from corrosion and scale buildup.
- Blow Down Vessel: To maintain the desirable level of dissolved solids in the boiler water, periodic discharge is required. This water is released at pressure and temperature, and needs to be adequately cooled and depressurized in a Blow Down or ‘Flash’ vessel.
- Water Treatment System: To extend the boiler’s life and enhance efficiency, the water used must be treated. This system typically includes water softeners and reverse osmosis (RO) units to remove minerals like calcium and magnesium, which can cause scaling.
- Chemical Monitoring Systems: These systems manage the precise addition of chemicals into the boiler, helping to maintain the correct water conditions, prevent corrosion, and ensure efficient operation.
- Combustion Fuel Types: Boilers can operate on various fuels. While Natural Gas and LPG are common, some systems also use biomass like wood chips. In electric boilers, electrical elements heat the water, offering a high-efficiency option without combustion emissions.
Installation Specific Components
Depending on the specific requirements and configurations of a site, additional components such as supplementary heat recovery systems, advanced control technologies, and custom configurations may be implemented to optimize the boiler system for specific operational needs and efficiency goals.
Each component is integral to the operation of a boiler system, contributing to its safety, efficiency, and longevity. Proper understanding and maintenance of these components ensure that the boiler operates reliably and at peak efficiency.
- Economizer: Installed in the exhaust flue, the economizer captures waste heat from the exhaust gases to preheat the incoming feedwater, significantly improving the boiler’s efficiency.
- Deaerator Tank: By heating the feedwater under high pressure, the deaerator removes dissolved gases such as oxygen and carbon dioxide, which can cause corrosion if left in the system.
- Heat Exchanger: A heat exchanger plays a crucial role in transferring heat from the combustion gases to another medium without direct contact, efficiently turning water into steam.
- Reverse Osmosis (RO) System: This system uses high pressure to push water through a semi-permeable membrane in the RO unit, effectively removing up to 99% of dissolved impurities, which is essential for protecting the boiler from scale and corrosion.
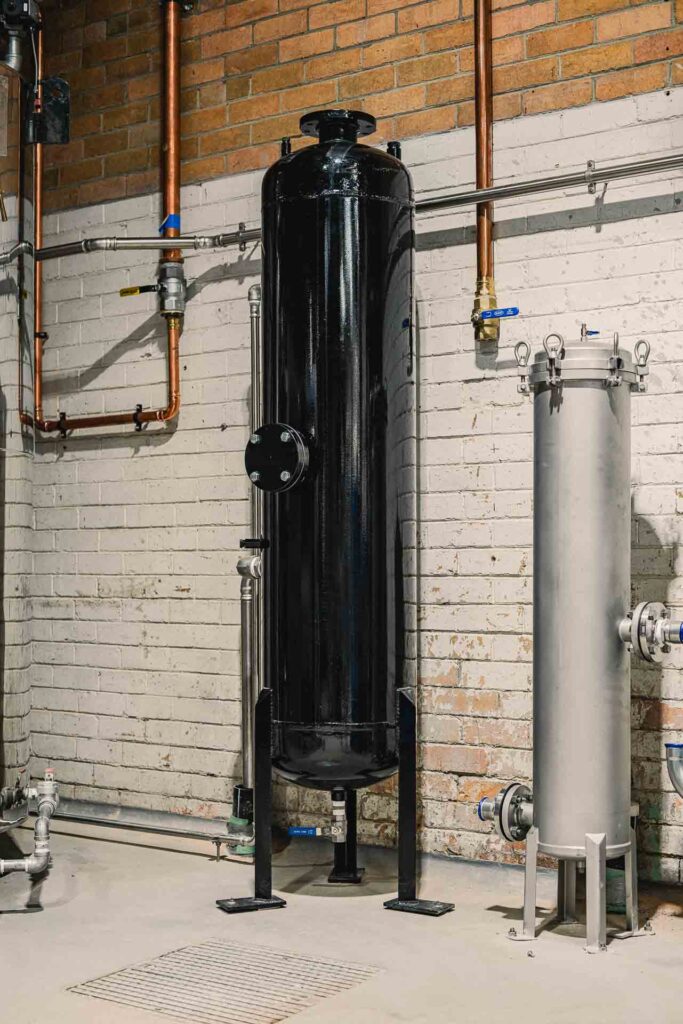
Firetube vs. Watertube Boilers
Understanding the differences between firetube and watertube boilers is crucial for selecting the right boiler for your application. Each type has unique operational mechanics, advantages, and uses that make them suitable for different scenarios.
Firetube Boilers
Firetube boilers are one of the oldest types of boilers. In these systems, combustion gases pass through one or more tubes that run through a sealed container of water. The heat from the gases is transferred through the tube walls to the water, heating it and creating steam.
- Operation: The operation of firetube boilers involves the combustion of fuel in a chamber (the firebox), after which the combustion gases pass through tubes that are surrounded by water. The heat exchange process heats the water to produce steam.
- History and Usage: Firetube boilers have powered some of the first steam locomotives and were extensively used during the industrial revolution. They are typically used in lower-pressure applications because the design limits their capacity to handle high pressures.
- Considerations: Although historically significant and quite efficient for low to moderate steam demand, firetube boilers are generally considered less efficient with high stored energy potential, which can pose safety risks in case of a malfunction. However, their design makes them easier to operate and maintain, which is why they remain popular for small to medium-sized industrial applications and heating purposes.
Watertube Boilers
In contrast, watertube boilers feature a system where water flows through tubes that are heated externally by the fire and combustion gases. This design is more suited for high-pressure applications.
- Operation: Water circulates inside the tubes and is heated by external gases, which are heated by a fuel source in a furnace. As the water in the tubes turns to steam, it remains contained within the tubes until it reaches the steam outlet.
- Capacity and Efficiency: Watertube boilers are capable of handling higher pressures and are therefore ideal for high-power and high-capacity industrial applications. Their ability to quickly handle changes in steam demand makes them more suitable for industries that require large amounts of steam at varying pressures.
- Safety and Risk: The design of watertube boilers offers a safer operation as they contain less water volume and have a lower risk of catastrophic failure. The structure allows them to not only operate at higher pressures but also achieve higher levels of thermal efficiency.
Comparative Advantages
- Efficiency: Watertube boilers are generally more efficient than firetube boilers because they can operate at higher pressures and their design minimizes heat loss.
- Safety: The design of watertube boilers provides a safer operation with less risk of explosion and faster response to changes in steam pressure and temperature.
- Suitability: Firetube boilers are often more suitable for smaller operations where the steam and pressure demands are lower, while watertube boilers are preferred for high-pressure and large-scale applications.
Choosing between a firetube and a watertube boiler ultimately depends on the specific needs of the process, including the required steam capacity, operational safety, and efficiency. At Concept Boiler Systems, we assess your needs to recommend the best type of boiler system that ensures efficiency, safety, and reliability.
Common Boiler Applications
Steam boilers are incredibly versatile and vital components in a wide range of commercial and industrial operations. Their ability to generate steam efficiently makes them indispensable in sectors where high-temperature and high-pressure steam is crucial.
Industrial and Commercial Applications
- Healthcare Facilities: Hospitals and other healthcare settings rely on steam for sterilizing equipment, heating buildings, and supplying hot water. The reliability of steam boilers is crucial in these environments to maintain health and safety standards.
- Educational Institutions: Universities and campuses often use steam boilers for central heating, hot water, and in some cases, for research purposes. These boilers must be reliable due to the constant demand throughout the academic year.
- Manufacturing and Chemical Plants: In manufacturing facilities and chemical plants, steam boilers provide process heat, essential for chemical reactions and other heat-related processes. The ability to maintain specific temperatures makes boilers essential for these applications.
- Food Processing Facilities: Steam plays a critical role in food manufacturing, from cooking and processing to sanitation and pasteurization. Steam’s ability to transfer heat efficiently and uniformly is crucial in maintaining the integrity and safety of food products.
- Breweries: Breweries use steam during the brewing process to heat mash and boil wort, which are critical steps in beer production. The precise temperature control afforded by steam is essential for producing high-quality beer.
- Automotive Industries: In automotive manufacturing, steam is used for processes like vulcanizing rubber, ensuring components meet stringent safety and quality standards.
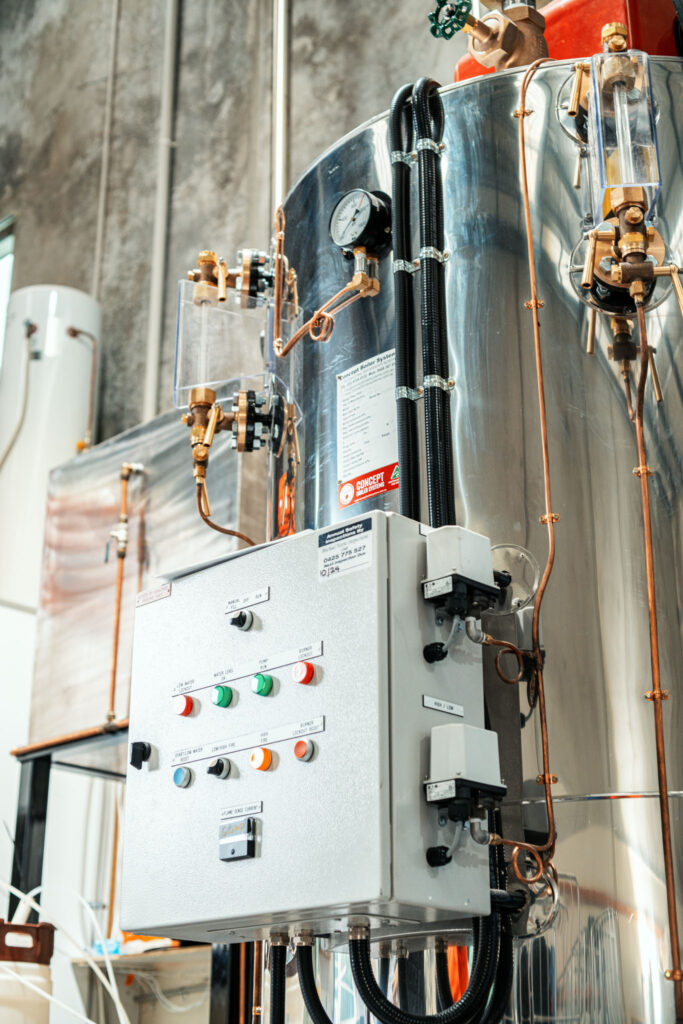
Boilers, Hot Water Heaters and Furnaces
In the realm of heating solutions, boilers, hot water heaters, and furnaces serve similar yet distinctively different functions. Each system is designed to meet specific heating needs, whether they’re for residential, commercial, or industrial environments. Understanding their differences is crucial for selecting the right heating solution for your requirements.
Boilers
Boilers are versatile heating systems that generate steam by heating water in a pressurized environment. The steam produced is then used in a variety of applications ranging from heating buildings to driving industrial processes. Here’s how they work:
- Functionality: Boilers heat water to create steam, which can be used for heating, power generation, and many other applications. The steam’s pressure, which directly correlates to temperature, can be precisely controlled to suit different industrial and commercial needs.
- Usage: In commercial and residential settings, steam from boilers is often distributed through radiators or HVAC systems for efficient space heating. Boilers can vary greatly in size and complexity, from small residential units to large industrial boilers designed for manufacturing plants.
High Temperature Hot Water Boilers
Unlike steam boilers, high temperature hot water boilers have a singular focus: heating water used in a commercial equipment that is suited to the properties of water, rather than steam. Typically, the water is circulated in a closed system, imparting heat to the process before being returned to the pressure vessel.
- Design: Most hot water heaters feature a tank where water is stored and heated by electrical elements or a gas burner. This hot water is then piped to faucets, showers, and appliances as needed.
- Function: The primary function of high temperature hot water boilers is to provide a reliable supply of hot water at a controlled temperature for commercial use, not for heating spaces or generating power.
Furnaces
Furnaces provide a solution for space heating by warming air instead of water. They are a common sight in homes and businesses where central heating is required.
- Operation: In a furnace, fuel is burned to heat air directly in a heat exchanger. This hot air is then blown through ducts that distribute the warm air throughout a building. This method of heating is effective for maintaining comfortable temperatures in living and workspaces.
- Control: The temperature of the air and the operation of the furnace are regulated by a thermostat, which ensures that the indoor environment remains within the desired comfort range.
Comparison Summary
- Boilers: Offer versatile applications beyond just heating, including driving machinery and processes in various industries. They are ideal for any application where steam or high-temperature water is required.
- Hot Water Heaters: Specialize in providing hot water for domestic and commercial uses and are simpler in design and operation. Ideal for consistent, everyday hot water use.
- Furnaces: Focus on heating air to warm interiors of buildings and are controlled via thermostats to maintain desired temperatures.
Each of these systems has its strengths and is suited to different tasks. Choosing the right one depends on your specific heating needs, the scale of your operations, and your efficiency requirements. At Concept Boilers, we specialize in providing tailored solutions that meet the diverse needs of our clients, ensuring optimal performance, efficiency, and reliability.
Efficiency: Fuel-to-Steam vs. In-Service
In the realm of steam boilers, efficiency isn’t just a desirable feature—it’s a critical measure of performance and cost-effectiveness. Understanding the different ways boiler efficiency is measured is essential for operators to optimize operations and reduce energy costs. The two primary standards for measuring boiler efficiency are fuel-to-steam efficiency and in-service efficiency.
Fuel-to-Steam Efficiency
Fuel-to-steam efficiency, commonly referred to by its broader term, Annual Fuel Utilization Efficiency (AFUE), gauges how well a boiler converts the energy in its fuel to steam. Specifically, it measures the percentage of energy turned into usable steam. This efficiency rating is particularly useful when assessing the combustion efficiency of the boiler:
- Definition: It quantifies the exact percentage of fuel energy that is successfully converted into steam.
- Limitation: While AFUE is an excellent measure of a boiler’s theoretical efficiency under specific conditions (typically full load), it doesn’t always reflect the operational reality. Boilers rarely operate at full capacity at all times due to varying demands throughout their use.
In-Service Efficiency
Given the practical usage patterns of boilers, in-service efficiency provides a more realistic measure of a boiler’s performance during regular operation:
- Practical Application: This metric considers the efficiency of the boiler not just under optimal conditions, but as it operates day-to-day, under normal load variations.
- Importance: In-service efficiency is critical for understanding and optimizing the real-world energy consumption and performance of a boiler system, taking into account the start-up, shutdown, and partial load conditions.
Boiler Turndown Ratios
An integral component related to in-service efficiency is the boiler’s turndown ratio, which measures the ability of the boiler to reduce its maximum output without shutting down. This flexibility is crucial for energy savings and adapting to fluctuating steam demands:
- Flexibility: A high turndown ratio means the boiler can operate effectively at a fraction of its maximum output, reducing unnecessary energy consumption when full steam output is not needed.
- Resource Conservation: By adjusting the output to match actual demand, high turndown ratios help conserve fuel and reduce wear on the boiler components, leading to longer service life and reduced operational costs.
Understanding these efficiency metrics and operational characteristics is vital for anyone involved in the management or selection of boiler systems. At Concept Boiler Systems, we design our products to not only meet but exceed these efficiency standards, ensuring that our boilers deliver maximum performance while minimizing energy and operational costs. This approach helps our customers achieve their productivity goals with optimal energy usage, aligning with sustainable operational practices.
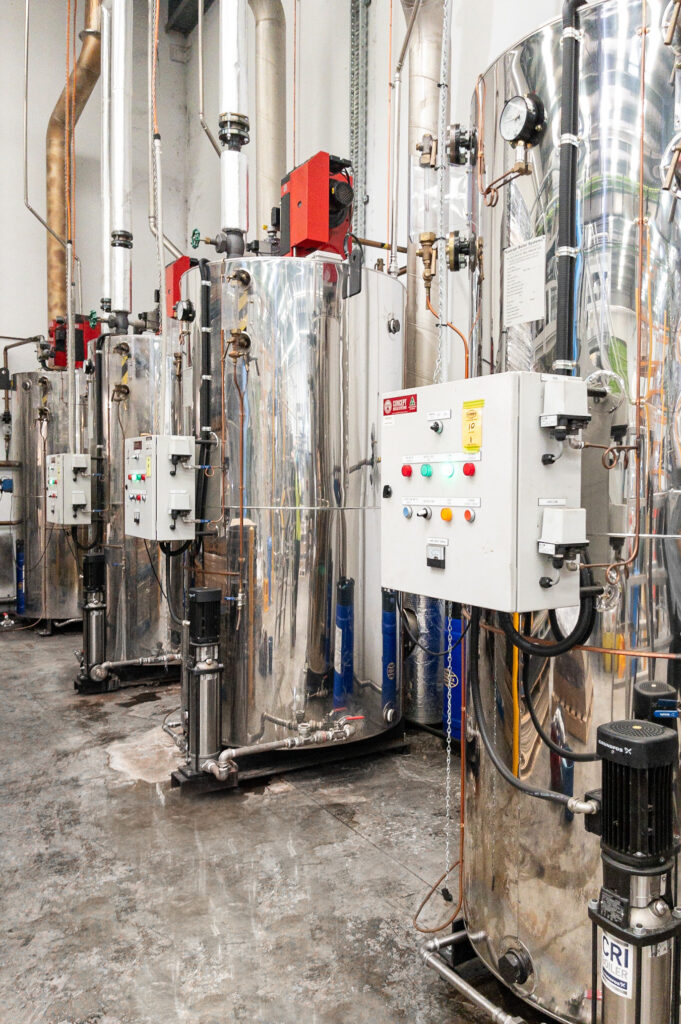
Efficiency and Design: Traditional vs. Modular Water Tube Boilers
- Traditional Firetube Boilers: While capable of meeting various industrial needs, traditional firetube boilers can be less efficient due to longer heat-up times and higher fuel consumption, particularly when large volumes of water are involved.
- Watertube Boilers: Compared to firetube boilers, watertube boilers are generally more efficient as they contain less water, reducing the energy required to start up and reach operating temperatures. Their design allows for quicker steam generation and better response to changes in steam demand.
- Modular Boiler Systems: For optimal efficiency, Concept Boilers recommends modular boiler systems. These systems consist of multiple small boilers that can be individually controlled and operated only when needed, significantly enhancing overall energy efficiency.
- Quick Start-Up: Typically, each module in our systems can start producing steam in less than fifteen minutes, allowing for rapid response to varying steam demands without the inefficiency of heating a large single boiler.
- Space Efficiency: Modular units are compact, requiring less room than traditional large boilers, which is particularly advantageous in facilities with limited space.
- Wear and Tear Management: The ability to rotate the use of different units within a modular system reduces wear and tear, extending the lifespan of each boiler.
- Fuel Savings: Individual boilers can be turned off when not in use, ensuring fuel is not wasted, thereby reducing operational costs.
- Reliability and Scalability: If one unit requires maintenance or fails, others continue operating, ensuring uninterrupted steam production. Additionally, the system can be scaled up by adding more units as needed, offering flexibility for future expansion.
By incorporating advanced designs that prioritize both environmental sustainability and operational efficiency, Concept Boiler Systems not only meets but exceeds modern performance expectations. Our commitment to innovation in boiler technology ensures that our clients benefit from lower operational costs, reduced environmental impact, and adaptable steam solutions that grow with their needs. Whether you are implementing a new system or upgrading an existing one, our modular water tube boilers offer a superior alternative to traditional models, making them the smart choice for a forward-thinking business.
Boiler Safety: Historical Overview and Modern Standards
The history of steam boilers is marked by both innovation and tragedy. In the early days of steam power, the absence of standardized safety protocols led to numerous boiler explosions, causing devastating injuries and loss of life. These incidents underscored the critical need for stringent safety standards and robust boiler design to ensure operational safety and reliability.
Historical Context and Evolution of Boiler Safety
- Early Challenges: Initially, boilers were prone to explosions due to poor construction quality and lack of effective pressure controls. Materials and engineering practices often failed to withstand the pressures and temperatures required, leading to catastrophic failures.
- The Grover Shoe Factory Disaster: This pivotal event occurred in 1905 when a boiler explosion at the RB Grover shoe factory in Brockton, Massachusetts resulted in significant loss of life and injuries. The disaster served as a wake-up call regarding the dangers of inadequate boiler safety standards.
- Regulatory Response: The aftermath of the Grover disaster spurred regulatory change, beginning with state-level regulations in Massachusetts. This eventually influenced national safety standards aimed at preventing such incidents.
- ASME and Boiler Safety Codes: The American Society of Mechanical Engineers (ASME) played a crucial role in developing safety standards. The first Boiler and Pressure Vessel Code, published in 1915, laid down guidelines that have evolved into a comprehensive framework covering various aspects of boiler operation and maintenance.
Modern Boiler Safety Standards in Australia
In Australia, boiler safety is governed by several specific standards that ensure the safe design, operation, and maintenance of boiler systems:
- AS1228 Pressure Equipment – Boilers: This standard outlines the requirements for the design and construction of boilers. It ensures that boilers are built to withstand the operational pressures and temperatures without failure.
- AS2593 Safety Management and Supervision Systems: This standard provides guidelines for the operation and management of boilers. It includes protocols for routine checks, operation procedures and safety measures to prevent accidents.
- AS3788 Pressure Equipment In Service Inspections: Regular inspections are crucial for maintaining boiler integrity and operation. This standard specifies the inspection requirements during the boiler’s service life to ensure ongoing safety and performance.
- AS4458 Pressure Equipment Manufacture: This standard ensures that the manufacturing process of pressure equipment adheres to safety and quality specifications, reducing the risk of defects that could lead to safety issues.
Safest Boiler Technologies Today
Modern boilers are designed with multiple safety features that virtually eliminate the risk of catastrophic failure:
- Improved Materials and Design: Advances in material science and engineering have significantly enhanced the structural integrity of boilers.
- Automated Control Systems: Modern boilers are equipped with sophisticated control systems that monitor pressure, temperature, and other critical parameters. These systems automatically adjust operations to maintain safe conditions and alert personnel to potential issues.
- Safety Valves and Protocols: Features like safety valves release excess pressure, preventing overpressure conditions that could lead to explosions. Regular safety drills and protocols ensure that operations staff are prepared to handle emergency situations effectively.
The evolution of boiler safety from its early hazardous days to the current standards is a testament to the engineering advances and regulatory frameworks that protect lives and property. At Concept Boiler Systems, we adhere strictly to these standards, incorporating cutting-edge technology and rigorous safety checks to ensure that our boilers are not only efficient but also exceed safety expectations. Our commitment to upholding these standards is integral to our mission of delivering reliable and safe boiler systems to our clients.
In the pursuit of industrial efficiency and operational safety, modern boiler designs in Australia have been significantly refined and enhanced. This improvement is critical for ensuring safety in commercial and industrial applications, where the potential consequences of boiler malfunctions can be severe.
Key Features of Modern Boiler Designs
Modern boilers incorporate advanced materials and design principles that make them more resilient and safer than ever before. These improvements include:
- Robust Construction: Today’s boilers are built with high-quality materials that withstand high temperatures and pressures. The use of corrosion-resistant materials helps prevent deterioration that could lead to leaks or structural failures.
- Advanced Monitoring Systems: Modern boilers are equipped with sophisticated monitoring systems that continuously track various operational parameters such as pressure, temperature, and flow rates. These systems enable early detection of anomalies that could indicate safety issues, allowing for prompt corrective actions.
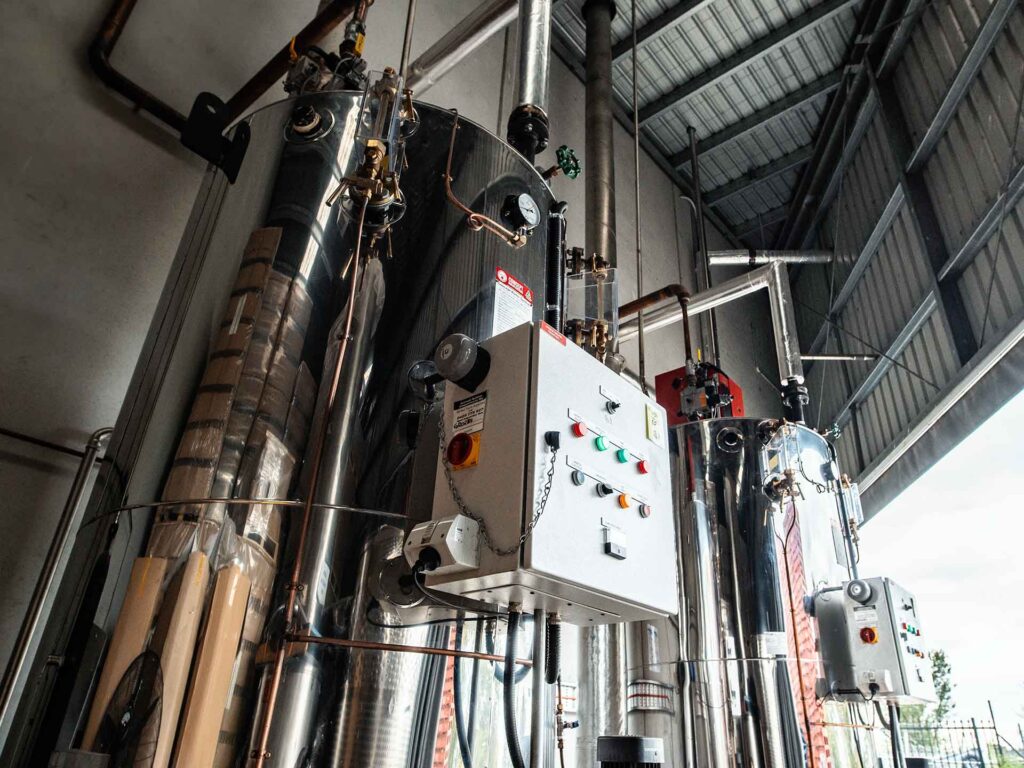
Watertube Boilers: The Safest Design?
Among the various boiler designs available today, watertube boilers are considered the safest, particularly for high-pressure applications:
- Low Water Content: Unlike firetube boilers, which contain large volumes of water at high temperatures, watertube boilers operate with less water content. This design reduces the energy stored in the boiler, thereby diminishing the risk and severity of explosions.
- Contained Failure: In the event of a failure, the design of a watertube boiler typically contains the damage within the tubes themselves. This containment reduces the likelihood of damage and injury compared to firetube boilers, where a failure might result in an outward explosion, posing greater risks to personnel and property.
Minimizing Thermal Shock
One of the critical considerations in boiler safety is the prevention of thermal shock:
- Definition of Thermal Shock: Thermal shock occurs when there is a rapid temperature change in the boiler, such as when cold water is introduced into a hot boiler. This can cause rapid expansion and contraction of the boiler material, leading to structural failure.
- Design Considerations to Prevent Thermal Shock: To minimize the risk of thermal shock, modern boilers are designed with features that regulate the temperature and pressure changes within the system. This can include improved control systems that carefully manage the water input and pre-heating techniques to temper incoming water.
- Operational Practices: Additionally, operational practices such as gradual heating and cooling cycles and maintaining consistent operational temperatures can help reduce the likelihood of thermal shock.
The design and operation of boilers have evolved significantly to enhance safety and efficiency. In Australia, adherence to stringent standards and the adoption of watertube boiler designs reflect the industry’s commitment to safety. By incorporating advanced materials, robust construction, and preventive measures against thermal shock, modern boilers provide a reliable and safe solution for commercial and industrial heating needs. At Concept Boiler Systems, we prioritize these safety features in our boiler designs, ensuring that each system we deliver meets the highest standards of safety and performance.
Boiler Maintenance & Monitoring: Adhering to Australian Standards
Steam boiler maintenance is not merely a recommendation—it is a critical necessity dictated by Australian Standard AS2593, which mandates regular service and safety checks. These checks are crucial for the safe operation of boiler systems and can vary in frequency from five-weekly to three-monthly, depending on the boiler type. Proper maintenance ensures optimal efficiency, enhances safety, and extends the lifespan of the boiler.
The Role of Maintenance
Regular and correct maintenance practices prevent potential incidents that can lead to significant machinery damage and, in extreme cases, catastrophic failures such as explosions. Beyond ensuring operational safety, effective maintenance strategies can also mitigate unexpected and often costly downtimes, thereby supporting continuous productivity.
Financial and Operational Benefits
While maintenance incurs costs, the investment in regular upkeep minimizes the likelihood of more substantial repairs or replacements down the line. A well-maintained boiler operates more efficiently, consuming fewer resources, which can significantly reduce energy costs over time.
Our technicians monitor your system for unexpected corrosion, and our annual boiler inspection service includes a thorough inspection of the unit by an independent boiler inspector. The optimal balance of Chemical Treatment will extend the life of your boiler and improve safety, while decreasing downtime and unexpected costs.
Key Maintenance Strategies
Best Practices for Maintaining Your Steam Boiler
Effective maintenance of steam boilers involves a combination of professional inspections and daily upkeep by the boiler operators. Below are some best practices to ensure the longevity and efficiency of your steam boilers:
Read the Owner’s Manual
The initial step in effective boiler maintenance is thoroughly understanding the specific operational and maintenance guidelines provided by the manufacturer. This ensures that the boiler is not only maintained correctly but also operated within its intended parameters to avoid unnecessary strain or damage.
Monitor Water Quality and Treatment Processes
Regularly checking and treating the water quality inside your boiler is crucial. Untreated water can lead to scale build-up and corrosion, which impede heat transfer and increase operational costs. Chemical treatments are essential to prevent these issues by controlling the levels of non-condensable gases and impurities.
Maintain a Rigorous Maintenance Schedule
Professional Inspections: Schedule regular inspections by qualified professionals to assess and maintain the safety and operational efficiency of the boiler.
Daily and Monthly Checks: Operators should perform daily and monthly inspections to monitor the condition of the boiler and identify any signs of wear or damage early.
Implementation and Record-Keeping
- Maintain detailed records of all maintenance activities, inspections, and treatments. This documentation is vital for tracking the boiler’s condition over time and ensuring compliance with safety regulations.
Maintaining a steam boiler in compliance with Australian Standards not only ensures operational efficiency and safety but also contributes to the reliability and longevity of the equipment. At Concept Boiler Systems, we emphasize the importance of rigorous maintenance protocols and provide our clients with detailed guidance and support to maintain their boiler systems effectively. This proactive approach to maintenance is designed to keep your steam boiler in optimal condition, safeguarding your investment and ensuring continuous productivity in your operations.